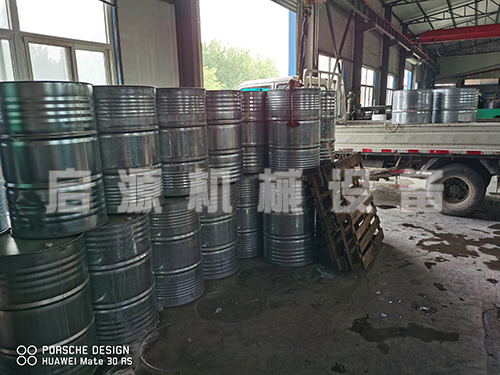
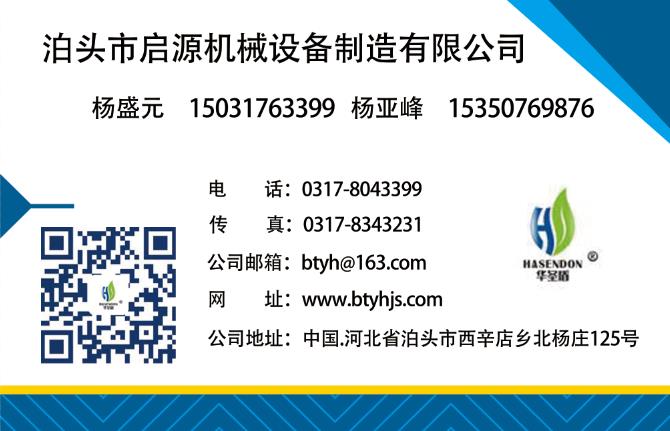
其一、真空浸渗工艺
1简单工艺流程
检查、零件除油清洗、干燥、零件放入浸渗罐并密封、抽真空、含浸、加压、取出零件漂洗、放置、加温固化、试压检验。
2各工步介绍
2.1零件除油清洗
主要目的在于去除零件表面的油污和灰尘,提高浸渗质量,防止油污及机械杂质带入浸渗液中,影响浸渗设备的稳定性。常用的除油清洗方法有溶剂清洗、表面剂清洗和碱性清洗剂清洗、复合清洗剂清洗、清洗等。
a.溶剂清洗一般是用汽油等有机溶剂。除油快,对金属无腐蚀性,但存在易燃、毒性大的缺点。不宜大批量生产和应用。
b.表面剂除油具有比较便宜、、对金属腐蚀性小等优点,但是对于严重油污清洗效果较差。
c.碱液清洗适用于表面油污较严重的工件,缺点是对金属有一定的腐蚀性,控制好其pH值和温度。
d.复合清洗剂清洗效果佳,它集表面剂及碱液清洗两种优点,只要控制好点数就可达到满意的清洗效果,这也是发展趋势。
零件在上述溶液中清洗后,取出经热水漂洗再在80一90℃下烘干,为提高浸渗效果,并防止大量水分进入真空泵,零件清洗后的烘干是非常重要的。
2.2抽真空
目的是将零件气孔、缩孔中的气体及杂质尽量吸出来,使微孔中充分保持的状态。这样能地使浸渗剂填满孔。否则浸渗剂渗入时,很可能残留空气使浸渗剂不能填满整个微孔。零件在使用过程中,由于温度的变化,微孔内残留气体将发生收缩或膨胀,破坏微孔中的浸渗剂固化物而导致重新泄漏。因此,抽真空在全部浸渗工序中是关键的一环。
一般保持真空度为50~80mm汞柱,真空延长10min后开始含浸加压。
2.3含浸加压
含浸指的是让整个已抽真空的零件完全浸没在浸渗剂里,让浸渗剂渗入到竖”的微孔中去,并尽可能填满它。紧接着加压,目的是把已进入微孔中的浸渗剂牢固地压进去,充满微孔。操作时要使浸渗剂高度淹没零件3一5cm,加压5一6kg/c㎡,并在此压力下延长10一15min,减压至2一3kg/c㎡,将浸渗液返回贮液槽中,恢复常压,取出零件漂洗。
2.4漂洗
被含浸处理零件取出后,立即在水中漂洗10一15s。
为了提高漂洗效果,应在漂洗过程中保持水温40~50℃,并加空气搅拌设施。但在操作时应根据具体情况控制水温及时间,防止过漂洗,影响浸渗效果。
2.5固化
固化分室温放置和加温固化两阶段。室温放置的目的是使浸入微孔中的浸渗液的水分慢慢地蒸发一部分,防止因急骤加热导致水分蒸发过急,渗入微孔,特别是较大微孔内的浸渗剂随气流冲出而造成泄漏,影响浸渗效果。为使浸渗剂固化物具有良好的耐水性能,零件放置后在80一90℃下固化1一2h。
其二、浸渗剂的封孔范围及渗漏标准、检验方法
浸渗剂的封孔范围是指浸渗剂封闭铸件气孔孔径大小的范围,这是一项影响浸渗效果的重要技术指标。目前国内常用浸渗剂的封孔范围在φ0.2一0.5mm。由于实际生产过程中铸件本身气孔、缩孔的孔径大小很难测量,一般采用气压法或水压法来判定铸件渗漏程度,并以此来判定是否需要重复两次浸渗处理。气压法是将零件装在特制夹具上,然后浸入水中,在铸件内腔通入气压为490kPa的压缩空气,保压1.5一3min,若每隔3s出现一个直径为smm左右的气泡者视之为滴漏;若气泡连续呈线性则称为线漏。水压法是将铸件置于特制密封夹具上,以压力为490kPa的水通入铸件内腔,保持2min,若每隔3s滴一水滴者称之为滴漏;若水流呈细线状则称为线漏。对于滴漏铸件,一般一次浸渗处理后就能达到耐压密封要求,对于线漏铸件采用两次浸渗处理才能达到耐压密封要求。对于两次浸渗后试压仍有渗漏的铸件,经解剖分析,它的气孔范围已经超过封孔范围,采用三次浸渗后合格率也仅有25%左右,因此第三次浸渗处理实际价值不高,不宜采用。
检查铸件浸渗效果一般有如下两种方法。
a.将浸渗后的铸件放在专用试验台架上,通以规定的压力,若无渗漏则为合格。
b.将浸渗的铸件放在沸水中煮2h,取出立即做耐压试验,若无渗漏为合格。此方法比较苛刻,且需时间较长,一般只在考察浸渗剂性能时使用,在日常生产时,只用前一种方法即可。
泊头市启源机械设备制造有限公司(http://www.btyhjs.com)从事无机浸渗设备、有机浸渗设备、气孔微孔浸渗处理产品已浸透到华北、西北、华南、东北的铸造行业,竭诚为您服务,并真诚希望与天下有识之士交流合作,携手发展,共创伟业!
原文链接:http://www.mzyin.com/chanpin/show-28823.html,转载和复制请保留此链接。
以上就是关于天津有机浸渗设备订做厂家~泊头启源厂家加工无机浸渗剂全部的内容,关注我们,带您了解更多相关内容。
以上就是关于天津有机浸渗设备订做厂家~泊头启源厂家加工无机浸渗剂全部的内容,关注我们,带您了解更多相关内容。